Speed Up Warehouse Orders with Atomix
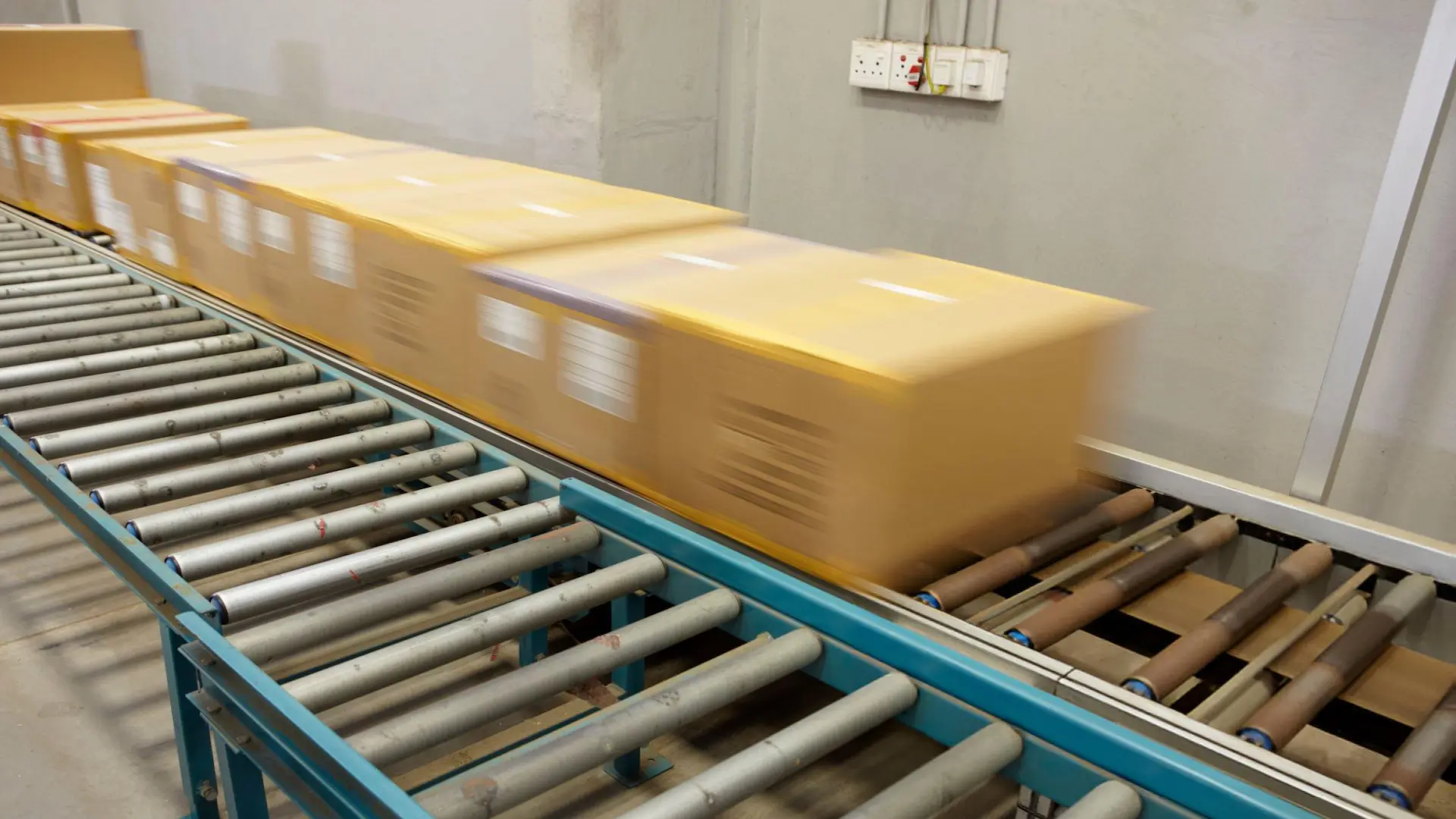
Fast and accurate order processing is one of the most important parts of warehouse order fulfillment. When orders take too long to fill or get delayed because of simple roadblocks, the ripple effect can frustrate customers and complicate your internal flow. Getting items from shelf to shipment quickly doesn’t just make your customers happy. It frees up space, keeps your team moving, and helps you manage inventory more confidently.
Speeding up warehouse order processing doesn’t have to mean huge changes. Often, it’s small tweaks to your layout, picking strategies, and systems that make the biggest difference. Whether you’re running a small setup or managing a larger facility, the goal remains the same. Less delay, fewer errors, and more orders out the door on time.
Optimize Warehouse Layout
Your workflow starts with the way your warehouse is set up. If your team is losing time zigzagging across rows or hunting for slow-moving products mixed in with popular ones, it may be time for a layout reset. A cluttered or disorganized layout can eat into output and cause unnecessary slowdown.
Think of your layout as a map that guides every movement. The fewer steps your staff takes, the more orders you can process. Start by sorting your inventory based on how often items are picked. Fast-moving products should be placed closest to packing stations. This cuts down footsteps and speeds up turnaround time.
Here are a few layout tips to consider:
- Place popular SKUs near shipping zones
- Use clear labeling on racks and bins to reduce mistakes
- Keep packing stations close to picking areas
- Make aisles wide enough for safe, easy movement
- Use vertical shelving for slower-moving or bulky inventory
Let’s say you’re storing seasonal items. Shorts and t-shirts in the summer should be positioned closer to the front picking zones. Off-season items like jackets can be shelved further back. This simple rearrangement can eliminate unnecessary steps and free up time.
An optimized layout also makes onboarding faster for new staff and simplifies restocking. When your team knows exactly where to go without second-guessing, their work naturally becomes faster and more efficient.
Implement Efficient Picking Strategies
The way your staff pulls products from storage can have a big impact on overall speed. Not every picking method works for every type of order, so choosing the right approach for your business setup is important.
Here are a few different strategies to try:
1. Batch Picking: Ideal when several orders contain the same items. Staff collects those items in bulk, then separates them into specific orders afterward.
2. Zone Picking: Employees are assigned to one specific area of the warehouse. Each one picks for their zone only, and a final order is assembled by combining items from each zone.
3. Wave Picking: Orders are grouped into timed waves based on delivery schedule or destination. This works well when you have busy shipping deadlines.
4. Pick-to-Light or Voice Picking: Technology guides workers to the right shelf using lights or voice commands. These tools speed up the process and cut down on mistakes.
Choosing the best strategy depends on your order pattern and inventory type. For businesses with lots of recurring item combinations, batch picking can provide fast results. If you’re handling a wide variety of items across many zones, zone picking often makes more sense. Try testing different methods to see which one cuts down processing time and stress during your busiest hours.
Utilize Warehouse Management Software
Keeping track of real-time inventory and order statuses is tough when you're relying on spreadsheets or disconnected platforms. A strong warehouse management system, or WMS, helps keep shipments on track and reduces wasted time.
Effective WMS software offers:
- Real-time inventory tracking
- Barcode scanning compatibility
- Automatic stock level updates
- Simple order status visibility
- Integration with your online store
- Custom reporting to evaluate performance
Let’s say you sell across multiple platforms. Instead of switching between systems to see where items are or if a product is out of stock, you can track everything in one place. This saves time for your staff and avoids double selling or shipping errors.
If your current setup feels slow or hard to manage, upgrading your software could be the fastest way to speed up your warehouse order fulfillment process. That one switch can make a noticeable difference in your day-to-day operations.
Train and Empower Your Staff
All the software and smart layouts won’t help much if your team isn’t confident in what they’re doing. Well-trained workers make decisions faster, complete tasks with fewer mistakes, and create a smoother work environment.
Training should be ongoing. Even experienced team members can benefit from refreshers and updates. Make it easy for employees to review procedures and ask questions when something feels unclear.
Some helpful training ideas include:
- Short, frequent refreshers on common picking and packing tasks
- Practice zones where staff can try new tools or methods
- Shadowing programs that match new employees with veterans
- Regular reviews that explore performance and target areas of improvement
- Open feedback loops so staff can share ideas or point out faults in the process
Staff work harder and smarter when they’re trusted. Invite them to speak up when they notice slow-downs or friction points. For example, a worker might point out that returns spike every Thursday. That could help you shift resources for better handling. Combining good training with staff input gives you a team that actively helps improve warehouse speed.
Leverage Automation Tools
Automation can give your warehouse staff more time to handle tasks that need focus. It doesn’t mean replacing team members. It means using machines or tools to cut out manual steps and keep orders flowing steadily.
There are lots of ways to do this. For example:
- Print-on-demand labels that save trips to a separate printer
- Conveyor belts that move boxes between zones
- Sorting machines organized by delivery region
- Smart scanners that update inventory the moment you pick an item
Automation doesn’t need to be all or nothing. You might start by adding a label printer to a busy packing station or using software that auto-generates pick lists. Your options grow as your volume grows. Start in the areas where your team constantly pauses or repeats the same task. That’s where automation brings real-time savings.
Getting the Most Out of Your Fulfillment Process
Speeding up warehouse order fulfillment is a process, not an overnight fix. But small changes stack up. A thoughtful warehouse layout, a smarter pick method, an upgraded WMS, regular training, and just the right amount of automation can take a slow system and turn it into a fast, dependable operation.
Look for the friction points. What keeps your team waiting? What tools feel clunky? Where do errors happen most? These are signs you’re ready for improvement. By taking a close look at every piece of your process, you can shorten the time between order and ship while making your team’s life easier. That means happier employees, faster turnaround time, and more satisfied customers.
Looking to enhance the efficiency of your warehouse operations? Explore how Atomix's innovative approach to warehouse order fulfillment can help you streamline processes, reduce delays, and deliver a better experience for your customers.
Talk with a team member and get $1,000 of order fulfillment credit*
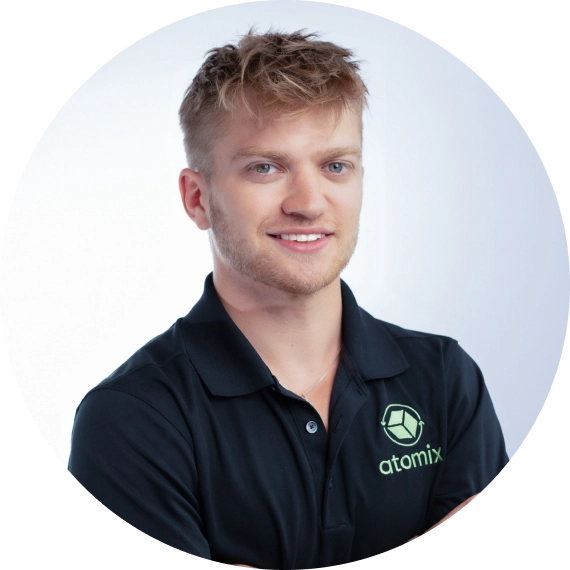
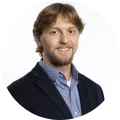
*$1,000 of credit is applied to customers account after Atomix fulfills their 500th order