Optimizing Your Supply Chain for Seasonal Demand Fluctuations
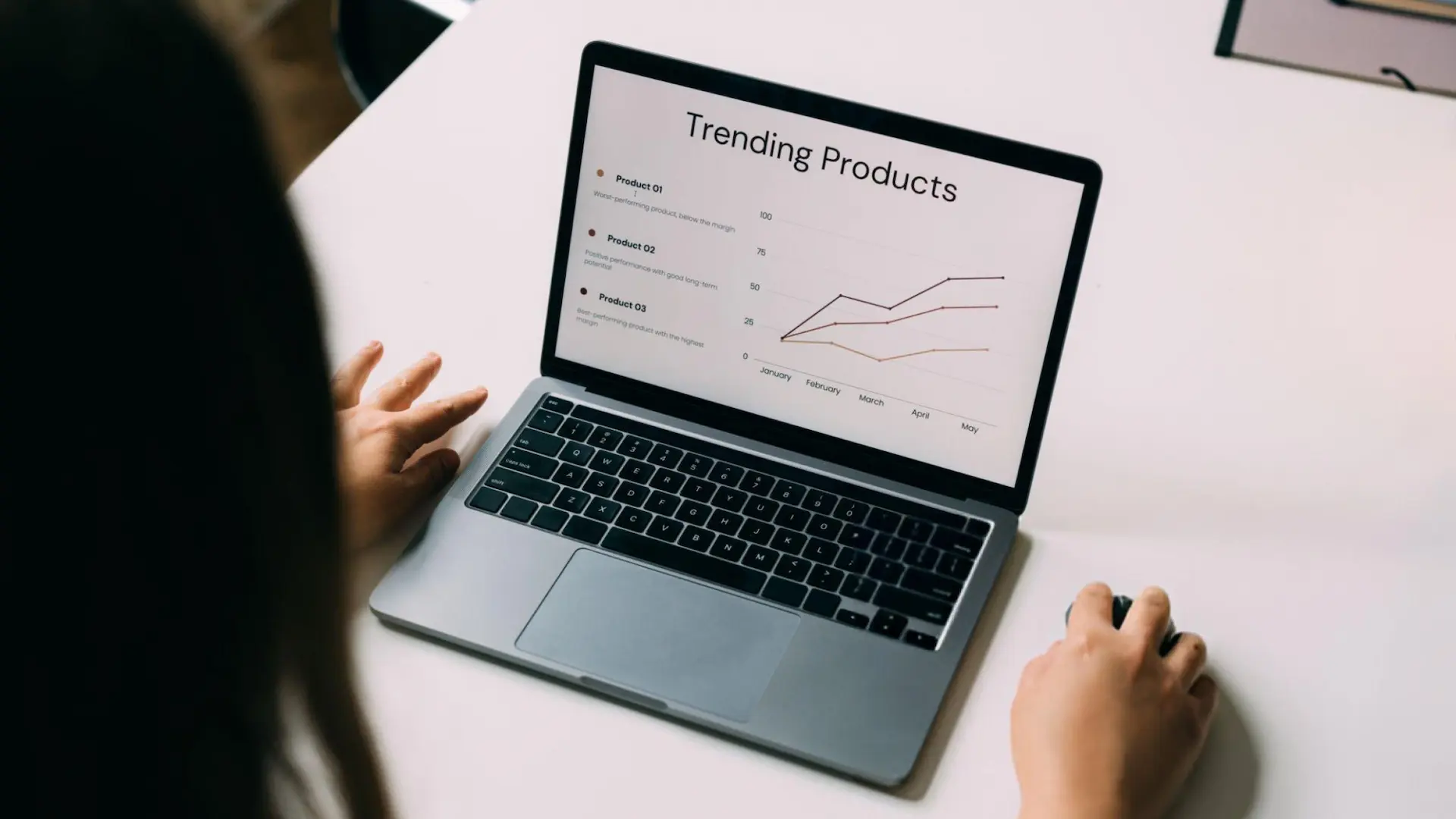
In the world of supply chain management, few challenges are as persistent or as important as adapting to seasonal demand fluctuations. Whether it's preparing for the holiday rush or managing the slowdown after peak seasons, supply chain managers need to be proactive to ensure they meet customer expectations without sacrificing cost efficiency.
Seasonal demand changes can affect everything from inventory optimization to transportation management, supplier relationships, and even staffing levels. By leveraging smart strategies such as demand forecasting, logistics coordination, and cross-functional collaboration, companies can stay agile and responsive, no matter the time of year. In this article, we’ll explore key strategies to optimize your supply chain for seasonal demand fluctuations, ensuring seamless operations and customer satisfaction.
Understanding Seasonal Demand Fluctuations in Supply Chain Management
Before diving into how to optimize your supply chain for seasonal demand fluctuations, it’s crucial to understand what drives these changes. Seasonal demand isn’t just about holidays like Christmas or Black Friday; it encompasses any predictable changes in buyer behavior based on time of year, sales patterns, or even weather conditions.
For instance, retailers might see surges in demand during summer or winter seasons, while manufacturers may experience increased order fulfillment for specific goods during the agricultural harvest season. Market trends and historical data analysis play a crucial role in identifying these periods of high and low demand, making them essential components of demand planning.
Key challenges posed by seasonal demand fluctuations:
- Demand variability: Predicting the exact volume of products needed during different seasons is difficult.
- Inventory optimization: Keeping too much stock risks waste, while insufficient stock can lead to lost sales.
- Supplier management: Aligning supplier capacity with seasonal spikes.
- Logistics coordination: Ensuring efficient transportation and delivery during peak times.
- Production planning: Balancing production rates with fluctuating demand.
Demand Forecasting and Its Role in Seasonal Supply Chain Optimization
One of the most effective ways to manage seasonal demand is through robust demand forecasting. By analyzing historical data, sales patterns, and market trends, businesses can forecast demand for each season with better accuracy. Demand forecasting helps with capacity planning, inventory management, and making more informed production decisions.
For instance, a retailer gearing up for the holiday season may use demand planning software to predict customer demand based on previous sales data and current market trends. This allows them to order the right amount of products and avoid excess inventory, which can lead to waste. Similarly, manufacturers can use trend analysis to anticipate a rise in production orders and prepare accordingly.
Steps for Effective Demand Forecasting:
- Leverage historical data: Analyze past sales data to identify patterns and predict future demand.
- Monitor market trends: Keep an eye on emerging trends in your industry that could influence customer buying habits.
- Incorporate customer insights: Use feedback and data from customer interactions to refine your forecasting.
- Use demand planning software: Implement software solutions that help integrate and analyze multiple data sources for more accurate forecasts.
By focusing on accurate demand forecasting, businesses can better manage inventory optimization and production planning for seasonal fluctuations.
Inventory Optimization and Safety Stock for Seasonal Peaks
Once demand forecasting has been established, the next step in optimizing your supply chain for seasonal demand fluctuations is to focus on inventory optimization. During peak seasons, ensuring you have the right amount of stock is critical for order fulfillment. Too little stock means missed opportunities and dissatisfied customers, while too much stock increases carrying costs and potential for obsolescence.
Safety Stock and Stock Replenishment Strategies
Maintaining safety stock is essential when preparing for uncertain demand. Safety stock is an extra buffer of inventory that protects against demand variability, ensuring product availability even when demand exceeds expectations. By combining demand forecasting with safety stock strategies, businesses can strike the right balance between stock availability and cost efficiency.
For example, during high-demand periods such as the holiday season, companies may opt for more frequent stock replenishment cycles to meet customer demand without holding excessive inventory. Cycle counting techniques can help businesses track and adjust their inventory levels to maintain accuracy throughout seasonal fluctuations.
Key Inventory Optimization Tips:
- Analyze historical demand patterns to calculate optimal stock levels.
- Adjust safety stock levels based on demand variability and lead times.
- Streamline stock replenishment to reduce excess inventory and avoid stockouts.
- Collaborate with suppliers to ensure timely deliveries during peak periods.
Supplier Management and Lead Time Considerations
A successful supply chain during seasonal peaks also depends heavily on strong supplier management. Lead time, or the time it takes for suppliers to deliver products, can significantly affect your ability to meet customer demand. During seasonal surges, suppliers may experience increased pressure to deliver on time, leading to potential delays.
To mitigate the risks, businesses should engage in collaborative planning with their suppliers well in advance of peak seasons. This collaboration should include setting realistic lead times, managing capacity planning, and ensuring that all parties are prepared to respond to sudden spikes in demand.
Best Practices for Managing Supplier Relationships During Seasonal Fluctuations:
- Build long-term partnerships with suppliers for better communication and reliability.
- Negotiate flexible contracts that accommodate seasonal demand changes.
- Consider alternative suppliers to reduce the risk of stockouts if one supplier cannot meet demand.
- Monitor lead times regularly and adjust ordering processes to account for potential delays.
Logistics Coordination and Transportation Management
During high-demand periods, businesses often experience strain on their transportation management systems. Efficient logistics coordination ensures that goods are moved quickly and accurately from warehouses to retailers or directly to customers.
A responsive supply chain is essential during these times. Peak season strategies should include increasing the capacity of logistics networks, optimizing shipping routes, and working with multiple carriers to prevent bottlenecks. For e-commerce businesses, multi-channel distribution is a powerful strategy for ensuring product availability across different platforms, from brick-and-mortar stores to online marketplaces.
Transportation management tips for seasonal peaks:
- Diversify transportation options to avoid reliance on a single carrier.
- Utilize data analytics to optimize shipping routes and reduce delivery times.
- Implement real-time tracking to keep customers informed and enhance service levels.
- Use automation technologies to speed up order processing and reduce manual errors.
Enhancing Supply Chain Agility and Flexibility
Supply chain agility refers to a company's ability to quickly adjust its operations in response to demand changes. In seasonal supply chains, this means being able to ramp up production, adjust shipping methods, or change inventory levels with minimal disruption.
Flexible staffing plays a big role in achieving supply chain agility. Many businesses hire temporary or seasonal workers to handle the increased workload during peak seasons. Investing in cross-training employees ensures that your workforce can quickly shift between roles as needed, maintaining productivity even during demand surges.
How to Increase Supply Chain Agility:
- Invest in automation technologies to streamline operations and reduce reliance on manual processes.
- Cross-train employees to increase flexibility in workforce allocation.
- Develop contingency planning to address potential disruptions, such as supplier delays or transportation breakdowns.
- Monitor performance metrics regularly to identify areas for improvement.
Risk Management and Contingency Planning
Seasonal demand fluctuations also present risks, such as stockouts, missed deliveries, or increased operational costs. This is where risk management and contingency planning come into play.
Having a well-defined contingency plan allows businesses to respond swiftly to unexpected disruptions. For instance, if a key supplier cannot deliver materials on time, a solid contingency plan would involve having backup suppliers or alternate shipping methods in place.
Key Aspects of Risk Management for Seasonal Supply Chains:
- Diversify your supply base to avoid over-reliance on a single supplier.
- Monitor real-time data to identify potential risks early.
- Plan for capacity shortages by partnering with flexible staffing agencies.
- Conduct regular reviews of your supply chain operations to refine and improve contingency plans.
Continuous Improvement and Performance Metrics
No supply chain optimization strategy is complete without a focus on continuous improvement. Tracking performance metrics during seasonal peaks helps businesses identify areas that need improvement, whether it’s in product availability, order fulfillment times, or transportation efficiency.
By analyzing data from past seasons, companies can continuously refine their processes, making their supply chain more resilient and responsive to future seasonal demand fluctuations. Tools like demand planning software, automation technologies, and trend analysis help businesses stay one step ahead.
Metrics to Track for Supply Chain Optimization:
- Order fulfillment times: Measure how long it takes to fulfill customer orders during peak seasons.
- Stockout rates: Track the frequency of stockouts to assess inventory management effectiveness.
- Supplier lead times: Monitor supplier performance to ensure timely deliveries.
- Transportation efficiency: Analyze shipping costs and delivery times to optimize logistics.
Conclusion
Optimizing your supply chain for seasonal demand fluctuations requires a blend of advanced planning, real-time responsiveness, and continuous improvement. From effective demand forecasting and inventory optimization to strong supplier management and agile logistics coordination, every component of the supply chain must be aligned with the goal of meeting customer demand efficiently and cost-effectively.
By focusing on key strategies like safety stock management, cross-functional collaboration, and contingency planning, companies can navigate the complexities of seasonal demand variability and maintain high service levels. The right technology, data-driven insights, and agile operations will position your business to thrive, even during the most unpredictable seasons.
Frequently Asked Questions (FAQ) on Optimizing Your Supply Chain for Seasonal Demand Fluctuations
How can I optimize my supply chain for seasonal demand fluctuations?
To optimize your supply chain for seasonal demand fluctuations, focus on demand forecasting by analyzing historical sales patterns and customer insights. Implement inventory optimization strategies, such as maintaining adequate safety stock, and work closely with suppliers to ensure flexibility in lead times and capacity planning. Additionally, enhance your logistics coordination and adopt automation technologies to streamline operations during peak periods.
What role does demand forecasting play in managing seasonal demand?
Demand forecasting is crucial in managing seasonal demand as it helps businesses predict customer needs based on historical data, sales forecasting, and market trends. Accurate forecasting allows for better production planning, stock replenishment, and overall supply chain agility, ensuring that companies can meet increased demand without overstocking or experiencing stockouts.
How can I improve supplier management during seasonal demand spikes?
To improve supplier management during seasonal demand spikes, focus on collaborative planning with suppliers to ensure they are aware of your demand forecasts. Negotiate flexible contracts and set realistic lead times to avoid delays. Additionally, consider diversifying your supplier base to minimize the risk of stockouts, and use performance metrics to monitor supplier reliability.
What are the best inventory management practices for handling seasonal demand?
Effective inventory management for seasonal demand involves adjusting safety stock levels to account for demand variability, using cycle counting techniques to maintain accurate inventory records, and optimizing stock replenishment schedules. Implementing demand planning software can help ensure you have the right products available when needed, reducing excess inventory and the risk of stockouts.
How do I maintain supply chain agility during seasonal peaks?
Maintaining supply chain agility during seasonal peaks requires investing in automation technologies, cross-training employees for flexible staffing, and developing contingency planning to address potential disruptions. Responsive supply chains allow businesses to adjust quickly to fluctuations in demand and maintain high service levels during busy periods.
Talk with a team member and get $1,000 of order fulfillment credit*
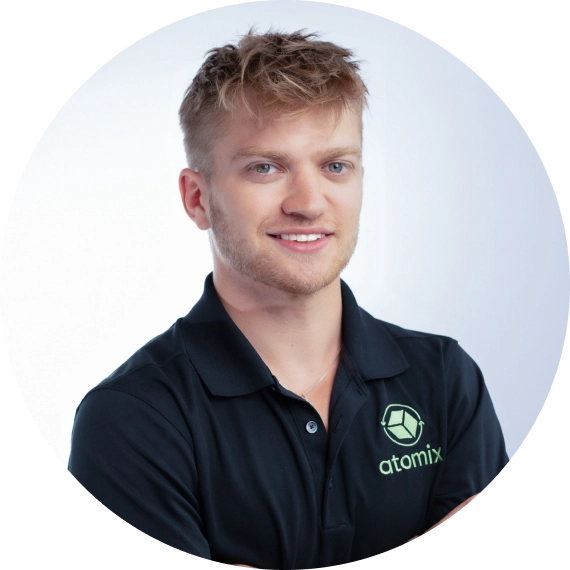
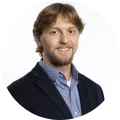
*$1,000 of credit is applied to customers account after Atomix fulfills their 500th order