Warehousing and Order Fulfillment: How They Work Together
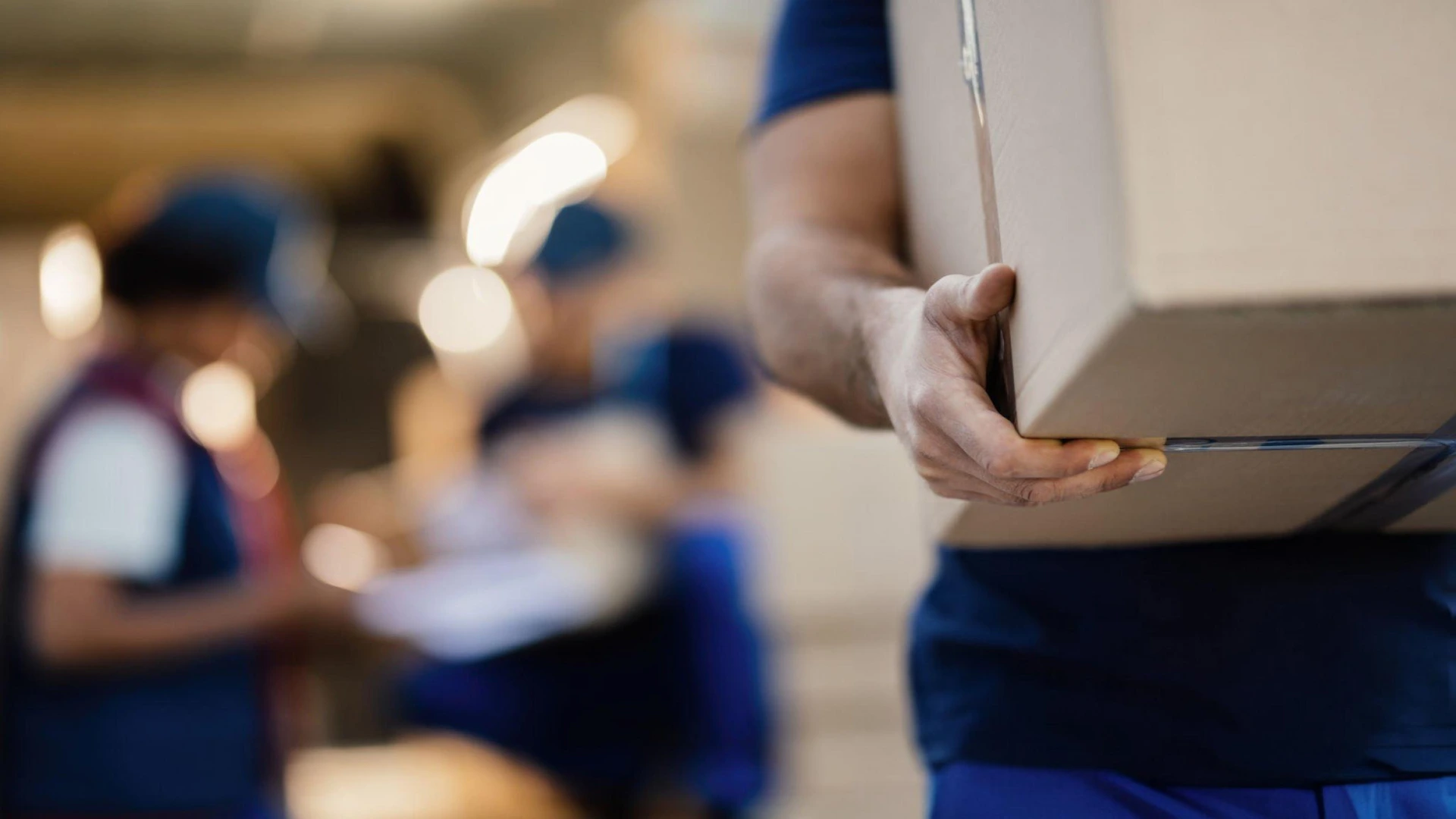
Efficient logistics are the backbone of ecommerce success. As brands scale, the relationship between warehousing and order fulfillment becomes a central driver of customer satisfaction and operational performance. When aligned, these two functions create a streamlined process that minimizes errors, reduces shipping times, and supports sustainable growth.
Brands aiming to stay competitive must move beyond fragmented logistics and invest in integrated solutions. Atomix Logistics specializes in unifying warehousing and fulfillment services to deliver measurable value across the supply chain. This article outlines how warehousing and order fulfillment work together, best practices for integration, and how brands can benefit from a seamless fulfillment strategy.
What Is Warehousing?
Warehousing refers to the storage, organization, and management of inventory before it is sold and shipped. A warehouse serves as a physical hub where goods are received, sorted, and prepared for the next stage in the supply chain.
Types of Warehouses for Ecommerce Brands
- Dedicated Warehouses: Reserved for a single business, offering full control but often requiring higher investment.
- Shared Warehouses: Used by multiple brands. This cost-effective model suits businesses with variable inventory levels.
- 3PL Warehouses: Operated by third-party logistics providers, offering scalability, staffing, and technology services under one roof.
For ecommerce fulfillment, having the right type of warehouse can improve inventory access, reduce delivery times, and support customer service goals.
What Is Order Fulfillment?
Order fulfillment refers to the complete process of receiving customer orders and delivering products. It includes multiple operational stages, each of which must be executed with precision.
Key Steps in the Order Fulfillment Process
- Order Receipt: Sales channels transmit customer orders to the fulfillment system.
- Picking: Staff or automated systems locate and collect the correct items from inventory.
- Packing: Products are packaged using branded materials, fillers, and documentation.
- Shipping: Items are handed off to carriers, and tracking details are sent to the customer.
- Returns Management: Returned products are evaluated, restocked, or disposed of as needed.
A streamlined order fulfillment process requires real-time inventory visibility and access to efficient shipping partners.
How Warehousing and Order Fulfillment Work Together
Warehousing and fulfillment are tightly interlinked. Poor coordination between these areas leads to delays, lost inventory, and customer dissatisfaction.
Inventory Storage
Inventory sits in warehouses until orders are placed. How well it is organized directly affects picking speed and accuracy.
Order Processing
When an order is received, the fulfillment team accesses the inventory within the warehouse to pick and pack items. The speed of this handoff is critical.
Technology Integration
Warehouse Management Systems (WMS) and Fulfillment Management Systems (FMS) connect inventory data and automate task flows:
- Generate real-time picking lists
- Track inventory levels as items move
- Sync with ecommerce platforms for up-to-date product availability
Shipping Coordination
Fulfillment centers align shipping operations with carrier networks. Proximity to major delivery zones improves ecommerce shipping times and reduces last-mile costs.
Returns Handling
Returned goods re-enter the warehouse system. Proper labeling, inspection, and restocking protocols support an efficient loop back into inventory.
Best Practices for Integrating Warehousing and Fulfillment
Strong warehouse and fulfillment integration can dramatically improve operational efficiency.
Centralize Data
Use integrated WMS and FMS platforms to ensure real-time inventory visibility and reduce mispicks.
Automate Key Processes
Deploy automation for:
- Picking and packing using barcode/RFID
- Inventory updates after shipments
- Label generation and shipping notifications
Automation increases throughput and reduces manual errors.
Optimize Warehouse Layout
Layout design affects how quickly items can be picked and packed:
- Store top-selling products near packing stations
- Use vertical shelving for space efficiency
- Implement bin locations with clear labeling
Regular Audits and Quality Checks
Perform frequent cycle counts and process reviews to identify discrepancies and adjust operations.
Scalable Infrastructure
Select warehouse and fulfillment solutions that can handle seasonal spikes, product launches, and long-term growth without sacrificing performance.
Technology’s Role in Modern Warehousing and Fulfillment
Technology now drives nearly every aspect of warehouse and fulfillment integration. Brands leveraging advanced systems gain more control, speed, and accuracy.
Key Technologies in Use
- Cloud-Based WMS: Enables remote access, system updates, and cross-platform visibility.
- Barcode & RFID Scanning: Accelerates receiving, picking, and packing processes.
- Ecommerce Platform Integration: Connects with platforms like Shopify, WooCommerce, and Amazon.
- Order Fulfillment Software: Automates shipping rules, generates reports, and tracks fulfillment KPIs.
- API Integrations: Connect systems across CRMs, sales channels, and analytics platforms.
These tools support real-time inventory tracking for fulfillment, automated workflows, and predictive restocking.
Benefits for Ecommerce Brands
For ecommerce brands, aligning warehousing and fulfillment isn’t just operational—it’s strategic.
Faster Shipping Times
Real-time coordination between inventory and fulfillment enables same-day or next-day shipping capabilities.
Lower Operating Costs
Automated workflows and optimized storage reduce labor, handling, and delivery expenses.
Fewer Fulfillment Errors
Integrated systems reduce manual entry, leading to fewer returns and increased order accuracy.
Stronger Customer Satisfaction
Fast, accurate deliveries improve customer loyalty and encourage repeat business.
Data for Smarter Decisions
Fulfillment software provides actionable data on order trends, product velocity, and inventory aging.
Choosing the Right Partners and Solutions
A reliable 3PL fulfillment provider offers end-to-end support, from warehouse space to last-mile shipping. Choosing the right partner is a key decision for brands looking to scale efficiently.
What to Look for in a 3PL Fulfillment Partner
- Technology Integration: Seamless API and platform connectivity
- Scalability: Ability to grow with your brand's needs
- Network Reach: Facilities located near key customer regions
- Specialization: Experience with ecommerce shipping, returns, and branded packaging
- Customer Support: Dedicated account managers and 24/7 monitoring
Atomix Logistics delivers on all these fronts with a proven track record in ecommerce fulfillment. From real-time inventory tracking to rapid shipping coordination, our team ensures your supply chain works as hard as your brand does.
Building a Competitive Edge with Integrated Warehousing and Fulfillment
Warehouse and fulfillment integration is no longer a nice-to-have—it’s a necessity for growth-focused brands. From improving ecommerce shipping performance to reducing fulfillment errors, brands that prioritize alignment between storage and delivery operations gain an edge in cost, speed, and customer trust.
Atomix Logistics helps ecommerce brands bridge the gap between inventory storage and customer delivery. With smart systems, real-time data, and scalable infrastructure, we provide warehouse fulfillment solutions that grow with your business.
Brands serious about optimizing logistics for long-term success should consider the benefits of a unified system supported by an expert 3PL partner. When warehousing and fulfillment work together, the result is a smoother operation, stronger customer relationships, and more reliable performance at scale.
FAQ: Warehousing and Order Fulfillment
What is the difference between warehousing and order fulfillment?
Warehousing involves the storage and management of inventory, while order fulfillment refers to the process of picking, packing, and shipping products to customers. Both functions must be closely aligned to ensure efficient ecommerce operations. When integrated properly, they reduce shipping times, minimize errors, and improve customer satisfaction.
How does a 3PL help with warehousing and order fulfillment?
A 3PL (third-party logistics provider) like Atomix Logistics manages both warehousing and order fulfillment under one service model. This includes inventory storage, real-time tracking, order processing, and shipping coordination. Partnering with a 3PL helps ecommerce brands scale faster without needing to build logistics infrastructure in-house.
Why is real-time inventory tracking important for order fulfillment?
Real-time inventory tracking helps prevent stockouts, overselling, and delays. It ensures that fulfillment teams always have an accurate view of available products, reducing picking errors and improving the order fulfillment process. Integrated systems like Warehouse Management Software (WMS) and Fulfillment Software provide this visibility.
What are the benefits of integrating warehousing and fulfillment systems?
Integration between warehousing and fulfillment systems improves efficiency by automating tasks, reducing manual errors, and accelerating order processing. Brands benefit from lower fulfillment costs, faster shipping, and better customer experience, all of which are critical for ecommerce growth and retention.
How do I choose the right warehouse and fulfillment partner for my ecommerce brand?
Look for a 3PL partner with experience in ecommerce fulfillment, scalable infrastructure, advanced technology integration, and a strong track record. Atomix Logistics offers warehouse and fulfillment integration designed for growing brands, complete with real-time tracking, flexible shipping options, and dedicated support.
Talk with a team member and get $1,000 of order fulfillment credit*
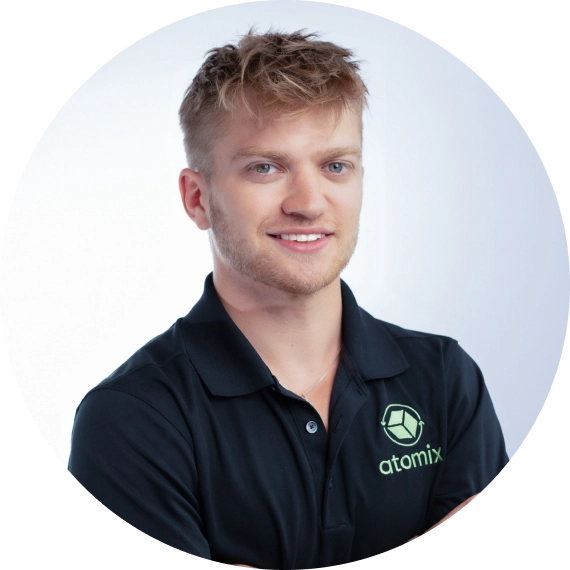
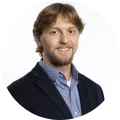
*$1,000 of credit is applied to customers account after Atomix fulfills their 500th order