Fulfillment Centers vs Warehouses: What's the Difference?
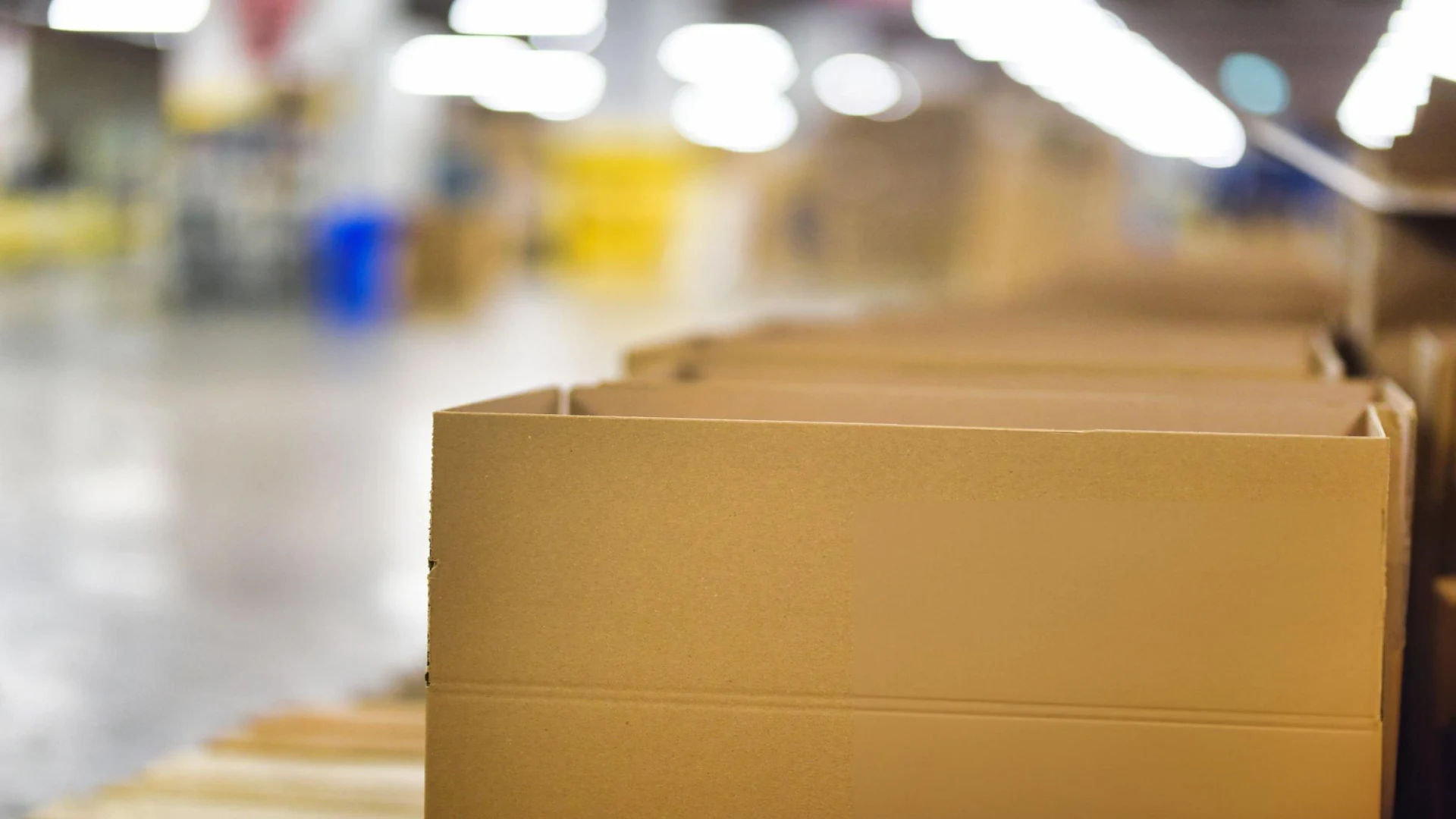
Understanding the difference between a fulfillment center and a warehouse is a critical step for ecommerce brands seeking to scale efficiently, reduce shipping delays, and improve customer satisfaction. As your business grows, the logistics model you choose can directly impact order processing speed, operational costs, and brand reputation.
Many ecommerce companies struggle to decide between using a traditional warehouse or a modern fulfillment center. Knowing how each one functions—and what they are optimized for—can help you make smarter logistics decisions that align with your customer expectations and growth targets.
This article breaks down the core differences between fulfillment centers and warehouses and positions Atomix Logistics as a trusted 3PL partner that helps ecommerce brands optimize their fulfillment operations with precision and speed.
What Is the Difference Between a Fulfillment Center and a Warehouse?
Understanding the fulfillment center vs warehouse comparison starts with their intended roles in the supply chain.
Fulfillment Centers: Built for Speed and Customer Satisfaction
Fulfillment centers are dynamic environments designed to manage the full scope of order fulfillment—from receiving inventory to picking, packing, shipping, and handling returns.
Key characteristics include:
- Fast Order Turnaround: Orders are shipped out quickly, often the same day.
- Real-Time Inventory Management: Integrated systems provide instant visibility into stock levels.
- Shipping Automation: Tools like order fulfillment software automate label creation, routing, and tracking.
- Customer-Focused: Returns processing, branded packaging, and shipping updates are part of the experience.
- 3PL Fulfillment Services: These centers are often operated by third-party logistics (3PL) providers like Atomix Logistics, allowing brands to outsource operations.
Warehouses: Focused on Storage and Bulk Distribution
Warehouses are static spaces focused primarily on long-term storage and basic inventory handling.
Key characteristics include:
- Bulk Inventory Storage: Ideal for holding large quantities of goods that move slowly.
- Manual Operations: Fewer systems and slower order processing.
- Limited Technology: Basic warehouse management systems (WMS) or spreadsheets are commonly used.
- Best for B2B: Suitable for shipping pallets or cases to retailers or distributors.
- In-House Fulfillment: Often used by brands managing logistics internally.
Choosing the Right Fit for Your Brand
Your business goals, customer expectations, and operational structure determine whether a fulfillment center or warehouse is the better choice.
Choose a Fulfillment Center If:
- Your brand offers direct-to-consumer ecommerce shipping.
- You need same-day or next-day delivery to stay competitive.
- Your team lacks time or space for manual packing and shipping.
- You're looking for 3PL shipping solutions that scale with you.
- You rely on real-time inventory management to prevent overselling.
Atomix Logistics provides tailored 3PL fulfillment for ecommerce brands, including inventory tracking, automated shipping, and returns processing. This all-in-one solution is ideal for fast-growing businesses aiming to improve delivery performance and customer retention.
Choose a Warehouse If:
- You need overflow space for slow-moving or seasonal goods.
- Your primary sales channels are wholesale or retail.
- Your fulfillment process is handled internally with long lead times.
- You're less concerned with speed and more focused on low-cost storage.
Technology Powers Fulfillment Centers Forward
Modern fulfillment centers gain their edge through technology, not just logistics staff.
Fulfillment Center Technology
- Automated Order Fulfillment Solutions: Reduce manual tasks, improving accuracy and speed.
- Integrated OMS/WMS: Systems that communicate in real-time across sales channels and inventory databases.
- Shipping Automation: Connects directly with carriers for instant label generation and routing.
- Real-Time Inventory Management: Prevents stockouts and ensures customers only buy what's available.
Warehouse Technology
- Basic Inventory Systems (IMS): Track pallet locations but lack real-time updates.
- Manual Order Prep: Slower and more prone to human error.
- Low Integration: May not connect with ecommerce platforms.
For ecommerce brands needing agile logistics, warehouses can’t match the speed, flexibility, or automation offered by a 3PL fulfillment center.
Comparing Costs: Fulfillment Centers vs Warehouses
Fulfillment Center Costs
- Charged per SKU storage, pick-and-pack, shipping, and returns.
- Technology and support are often bundled with service.
- Labor and space costs are offset by automation and shipping volume discounts.
Warehouse Costs
- Typically charged by the square foot or pallet position.
- Lower fixed costs but less scalable.
- Additional costs for staff, shipping prep, and technology must be accounted for separately.
When evaluating fulfillment center vs warehouse cost comparison, fast-moving ecommerce brands often find that 3PL services reduce overhead and improve profit margins by minimizing delays and errors.
The Customer Experience Advantage
Fast delivery, accurate packaging, and simple returns have become non-negotiables for online shoppers.
Fulfillment Centers Offer:
- Improved Delivery Speed: Speed is critical for repeat purchases and customer loyalty.
- Enhanced Customer Satisfaction: Branded packaging, tracking notifications, and easy returns.
- Reduced Shipping Errors: Automated processes mean fewer manual mistakes.
Warehouses Offer:
- Basic packing and dispatch (if handled in-house).
- Limited customization or branding.
- Slower returns processing and fewer service touchpoints.
For brands focused on building a strong reputation, the fulfillment center benefits for ecommerce brands go far beyond logistics—they impact customer lifetime value and retention.
Scalable Fulfillment for Growing Ecommerce Brands
Scaling requires more than extra inventory space. It demands logistics infrastructure that grows with demand, supports multiple sales channels, and adapts quickly to market changes.
Atomix Logistics supports ecommerce brands with:
- Scalable Fulfillment Solutions: Adjust resources to match seasonal or promotional surges.
- 3PL Fulfillment Center Technology: Connects with Shopify, Amazon, WooCommerce, and more.
- Inventory Tracking for Ecommerce Brands: Prevents overselling and stockouts across all platforms.
- Shipping Automation in Fulfillment Centers: Handles everything from carrier selection to customs documentation.
This technology-first approach creates a clear competitive advantage with fast order processing, especially in crowded ecommerce markets.
Decision Framework: Fulfillment Center or Warehouse?
Here’s a simplified guide to help you choose the right solution for your brand:
Use a Fulfillment Center If You:
- Ship 100+ orders per day directly to consumers.
- Rely on multiple ecommerce platforms.
- Want to improve delivery speed and accuracy.
- Prefer to outsource logistics to a 3PL like Atomix Logistics.
Use a Warehouse If You:
- Store inventory in bulk with limited order processing.
- Ship pallets to retail locations or distribution centers.
- Don’t need rapid turnaround or automation.
- Have internal logistics teams managing dispatch manually.
Aligning Fulfillment With Your Brand’s Growth Strategy
The decision between a fulfillment center and a warehouse should be aligned with your brand’s operational goals, customer expectations, and sales model. For ecommerce and direct-to-consumer businesses, fulfillment centers offer speed, automation, and technology that warehouses simply don’t provide.
Partnering with an experienced 3PL fulfillment provider like Atomix Logistics ensures your logistics operations are always ready to meet demand, reduce shipping errors, and deliver on customer promises.
Whether you’re just getting started with ecommerce fulfillment or scaling into new markets, Atomix Logistics gives you the infrastructure, tools, and expertise to grow without friction.
Frequently Asked Questions (FAQ)
What is the difference between a fulfillment center and a warehouse?
A fulfillment center focuses on picking, packing, and shipping individual customer orders, often for ecommerce brands. A warehouse is designed for long-term bulk storage and typically serves B2B operations or slower-moving inventory. Fulfillment centers are optimized for fast order processing and customer delivery, while warehouses support inventory holding and distribution.
Should my ecommerce brand use a fulfillment center or a warehouse?
If your brand ships directly to customers and relies on fast, accurate delivery, a fulfillment center is the better choice. Warehouses are ideal for bulk inventory storage or when fulfillment is handled internally with less urgency. Ecommerce brands benefit more from the speed, automation, and customer-focused services of a fulfillment center.
How does a 3PL fulfillment center help ecommerce businesses scale?
A 3PL fulfillment center like Atomix Logistics provides technology-driven services that automate shipping, track real-time inventory, manage returns, and integrate with ecommerce platforms. This allows brands to reduce operational overhead, speed up delivery times, and scale without needing to invest in their own logistics infrastructure.
What are the cost differences between fulfillment centers and warehouses?
Fulfillment centers typically charge for storage, pick-and-pack services, shipping, and returns. Warehouses often charge flat storage fees, with additional costs for labor or logistics handled separately. While fulfillment centers may seem more expensive upfront, their automation and efficiency often lower total fulfillment costs for high-volume brands.
Can a fulfillment center improve my customer satisfaction and delivery speed?
Yes. Fulfillment centers are built to handle fast, accurate shipping with minimal errors. With automated systems, branded packaging, and integrated returns processing, they improve both delivery speed and customer experience—two key factors in driving repeat business and positive reviews.
Talk with a team member and get $1,000 of order fulfillment credit*
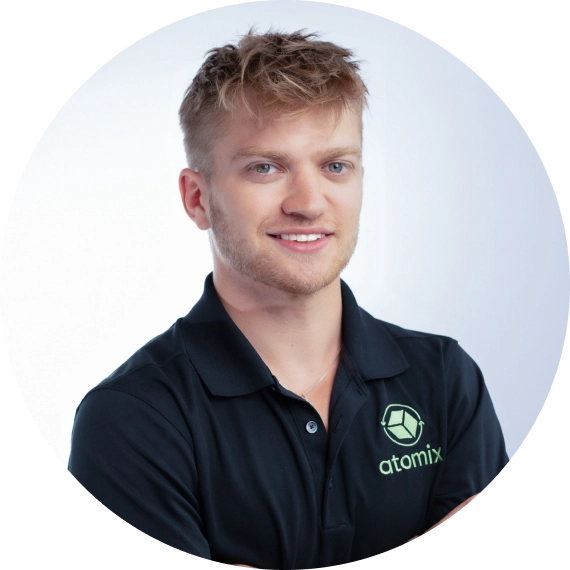
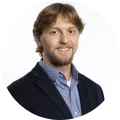
*$1,000 of credit is applied to customers account after Atomix fulfills their 500th order