How Does Atomix Optimize the Order Fulfillment Process?
.webp)
The Order Fulfillment Process can be one of the most manual and time-consuming processes for emerging brands.
We developed our Micro-Pod Model to Design, Automate and Optimize the end-to-end order fulfillment process for ecommerce brands. With purpose-built operations to increase productivity and profitability for emerging brands, brands can grow and scale without sacrificing the customer experience.
- Here’s a Step-by-step Guide to the Order Fulfillment Process.
- Here’s how we will estimate your costs with our Brand Preferences Form.
- Here’s the Onboarding Checklist
Inventory Allocation
First, our system calculates the optimal positioning of inventory.
The system is based on four primary inputs:
After calculating the impact of each input, Atomix positions inventory within the Micro-Pod and the excess inventory in the Back Stock.
By positioning the right amount of inventory in the Pod, we reduce long walking patterns typically found in a warehouse’s daily operations. We found these to be naturally inefficient. As a result, our model leads to more optimal workflows, a lower probability of risk from inaccurate picking, and ultimately lower operating costs for our customers.
By maximizing the storage bins within the Pod, we are able to store the right amount of inventory, reduce “wasted” space, and as a result, lower our customers’ total operating costs.
Real-time Customer Support
Second, we provide direct visibility to the hands-on team that handles daily operations. With dedicated Pod Managers (Warehouse Managers), we eliminate the potential loss of revenue from slow, outsourced customer support teams which exist in the 3PL market.
Explore how the Micro-Pod Model Designs, Automates, and Optimizes the order fulfillment process or speak with our team here!
Talk with a team member and get $1,000 of order fulfillment credit*
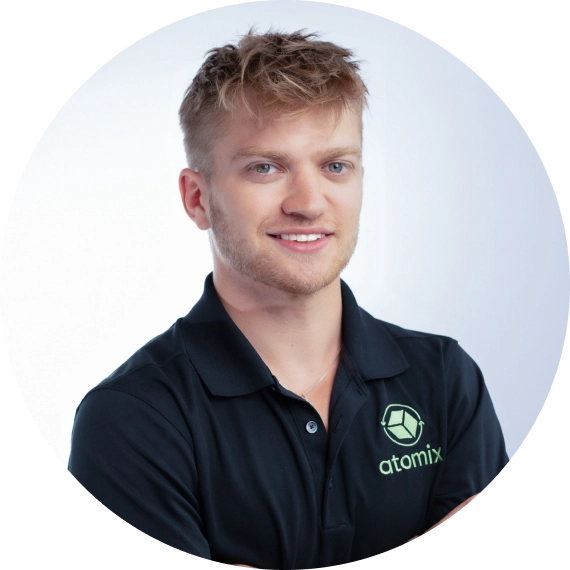
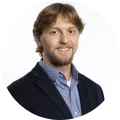
*$1,000 of credit is applied to customers account after Atomix fulfills their 500th order