Order Fulfillment Process: From Picking to Shipping
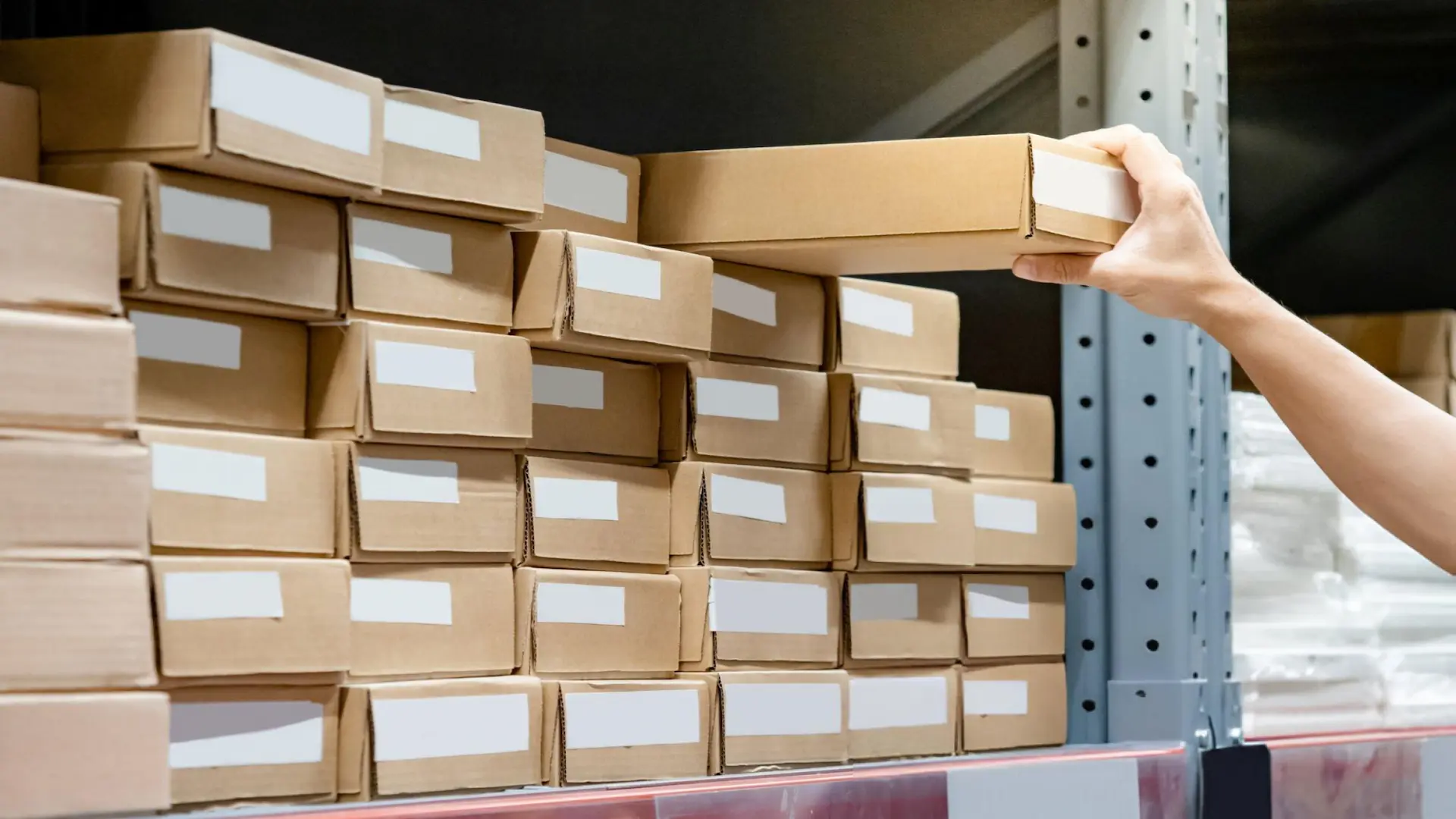
Efficient order fulfillment is the backbone of any successful ecommerce brand. With rising consumer expectations for fast and accurate delivery, brands can no longer afford delays, inventory mistakes, or poor packaging. Every touchpoint in the order fulfillment process—from receiving goods to shipping and returns—impacts customer satisfaction, cost management, and long-term loyalty.
Partnering with a trusted 3PL like Atomix Logistics helps brands implement streamlined workflows powered by advanced technology, offering a powerful advantage in the competitive ecommerce space. Atomix Logistics delivers comprehensive fulfillment services, giving brands the tools they need to grow faster, lower operational expenses, and deliver consistent customer satisfaction.
The Steps of the Order Fulfillment Process
Understanding the full lifecycle of the order fulfillment process helps brands identify where delays, errors, or inefficiencies can occur. Each stage requires precise coordination between systems, people, and processes.
1. Receiving Inventory
Before fulfillment can begin, inventory needs to be properly received and recorded. This stage lays the groundwork for accurate inventory management.
Inspect deliveries for accuracy and damage
- Every incoming shipment must match the purchase order. Incorrect counts or broken products lead to order delays and unhappy customers.
Update inventory systems in real-time
- Atomix Logistics uses integrated order fulfillment software and warehouse management systems (WMS) to reflect stock levels instantly, minimizing overselling or backorders.
Organize for efficient put-away
- Items are labeled, categorized, and directed to optimal storage locations within the warehouse using barcode or RFID systems.
2. Storage and Organization
Effective storage helps speed up order picking and packing, saving time and reducing error rates.
Use racking systems designed for SKUs
- Popular SKUs are stored in high-access zones. Atomix’s fulfillment center operations are designed around smart slotting logic.
Track inventory by location
- Every item has a designated bin, shelf, or pallet location, tracked in real time. This allows quick retrieval and reduced picker travel time.
3. Order Processing
Once a customer places an order, it's processed by software that connects the ecommerce store, WMS, and shipping partners.
Order validation and fraud check
- Orders are automatically screened for payment issues or anomalies before processing begins.
Generate pick lists and instructions
- Atomix’s system creates optimized pick paths, bundling multiple orders into efficient batch picks.
Sync stock levels across platforms
- Multichannel brands benefit from Atomix’s unified inventory updates across Amazon, Shopify, and other platforms.
4. Order Picking
Order picking is a critical step that directly affects fulfillment speed and accuracy.
Use of barcode scanners or RFID devices
- Atomix equips its staff with scanning tools to confirm correct item selection.
Voice or light-guided picking
- Advanced technologies reduce human error, especially for high-volume SKUs.
Batch and zone picking strategies
- By assigning pickers to zones or consolidating similar orders, Atomix minimizes warehouse walking time.
5. Order Packing
Once items are picked, they move to packing stations.
Right-size packaging for each order
- Atomix uses automated systems that select the ideal box size to reduce shipping costs and prevent damage.
Include branded materials and packing slips
- Ecommerce brands often include thank-you notes, coupons, or custom inserts. Atomix supports these brand experiences.
Secure packaging techniques
- Fragile items are protected with bubble wrap, corrugated inserts, or air pillows. Correct packaging reduces returns and replacement costs.
6. Shipping Orders
Fast and accurate ecommerce shipping is non-negotiable for today’s consumers.
Shipping label automation
- Atomix integrates with major carriers to auto-generate labels based on service level and cost.
Carrier selection and rate shopping
- The system automatically chooses the best shipping method to balance speed and budget.
Tracking and notifications
- Customers receive tracking links as soon as the order ships, building confidence and transparency.
7. Returns Management
A flexible and accurate returns process helps build loyalty and protects inventory accuracy.
Easy return initiation
- Atomix supports branded return portals, simplifying the process for end customers.
Inspection and restocking
- Returned items are assessed, restocked if eligible, or flagged for refurbishment or disposal.
Inventory updates and reports
- All returns are logged and synced with the brand’s inventory system to keep stock levels current.
Technology Driving Fulfillment Efficiency
Atomix Logistics leverages advanced systems that bring speed, visibility, and control to the order fulfillment process.
Key Tools Used by Atomix:
Warehouse Management Systems (WMS)
- Central to coordinating pick paths, storage logic, inventory visibility, and staff productivity.
Enterprise Resource Planning (ERP) Integration
- Syncs inventory, orders, and accounting across platforms, providing a unified source of truth.
Real-Time Inventory Management
- Every inventory movement—receiving, picking, restocking—is tracked in real-time, allowing brands to forecast demand accurately.
Shipping Label Automation
- Atomix’s software integrates with FedEx, UPS, USPS, DHL, and regional carriers, saving time and optimizing cost.
Best Practices to Streamline Fulfillment
Brands partnering with a 3PL fulfillment expert like Atomix benefit from proven workflows that reduce errors and delays.
Strategic Fulfillment Practices:
Data-driven decision making
- Atomix monitors key performance indicators like order accuracy, cycle time, and cost-per-order to drive continuous improvement.
Optimized warehouse layout
- Items are positioned based on order frequency. High-volume products sit near packing stations for faster access.
Standardized packaging workflows
- Packing protocols prevent overpacking or under-protecting items, keeping shipping costs under control.
Staff training and accountability
- Pickers, packers, and warehouse leads are trained on processes, tech tools, and service goals to maintain consistency.
How Fulfillment Impacts Brand Experience and Growth
Efficient ecommerce order fulfillment doesn't just reduce cost—it drives repeat sales, referrals, and loyalty.
Customer-Focused Outcomes:
Faster shipping improves satisfaction
- Atomix's nationwide fulfillment network and 2-day shipping options increase customer retention.
Fewer errors = happier customers
- With accurate picking and packing, return rates drop, and customer reviews trend positive.
Real-time updates keep buyers informed
- Automated tracking updates and branded delivery notifications increase confidence and reduce support tickets.
Easy returns protect brand trust
- Frictionless return policies, backed by fast restocking, show customers that their satisfaction is a priority.
Brands that deliver fast, accurate, and seamless fulfillment experiences build trust. That trust translates into stronger margins and long-term revenue.
Why Brands Choose Atomix Logistics
For ecommerce brands looking to scale, Atomix Logistics offers more than just 3PL shipping or a warehouse for ecommerce brand operations.
What Sets Atomix Apart:
Technology-first fulfillment services
- Atomix uses AI-driven workflows, real-time dashboards, and API integrations to sync with your ecommerce platforms.
Customizable solutions
- Whether you're shipping apparel, cosmetics, electronics, or subscription boxes, Atomix adapts to your needs.
National reach with fast delivery
- Multiple fulfillment centers across the U.S. support 1- to 2-day delivery zones.
Scalable and flexible operations
- From 1,000 to 100,000 orders per month, Atomix supports growth without service disruption.
Customer-first support team
- A dedicated client success team ensures responsive service, weekly reporting, and continuous optimization.
Gaining a Competitive Edge with Optimized Fulfillment
The difference between a one-time buyer and a loyal customer often comes down to fulfillment performance. Brands that commit to optimizing the fulfillment process steps, backed by reliable technology and expert partners, outperform the competition.
With Atomix Logistics as your fulfillment partner, your brand gains the infrastructure and insight needed to manage costs, boost delivery speed, and scale profitably. Whether you're looking to reduce fulfillment costs, improve ecommerce shipping, or implement real-time inventory management, Atomix has the systems and experience to support your vision.
Frequently Asked Questions About the Order Fulfillment Process
What are the main steps in the order fulfillment process?
The order fulfillment process includes receiving inventory, storing products, processing orders, picking and packing items, shipping to customers, and managing returns. Each step plays a crucial role in maintaining fast, accurate, and cost-effective delivery. Companies like Atomix Logistics streamline each phase with advanced technology and optimized workflows.
How can ecommerce brands improve order picking accuracy?
Brands can improve picking accuracy by using barcode scanning, RFID technology, and voice-guided picking systems. Partnering with a 3PL like Atomix Logistics enables access to optimized warehouse layouts, batch picking strategies, and real-time inventory data—all of which reduce errors and improve efficiency.
Why is a 3PL important for ecommerce fulfillment?
A 3PL (third-party logistics provider) like Atomix Logistics helps ecommerce brands scale faster by handling warehousing, inventory management, packing, shipping, and returns. This allows brands to focus on marketing and product development while delivering faster shipping and improved customer experiences.
How does technology enhance the fulfillment process?
Order fulfillment software, warehouse management systems (WMS), and shipping automation tools help brands speed up operations, reduce manual errors, and maintain accurate inventory. Atomix Logistics leverages these tools to offer real-time tracking, automated shipping labels, and seamless ecommerce platform integrations.
What are the best practices for reducing shipping delays in fulfillment?
To reduce shipping delays, brands should maintain real-time inventory visibility, automate order processing, optimize warehouse picking paths, and work with reliable 3PL fulfillment partners. Atomix Logistics ensures fast shipping by strategically locating fulfillment centers and using intelligent carrier selection tools.
Talk with a team member and get $1,000 of order fulfillment credit*
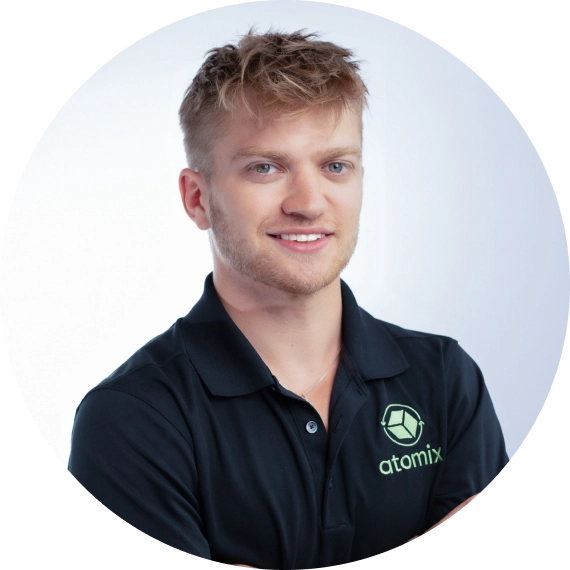
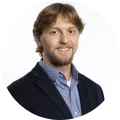
*$1,000 of credit is applied to customers account after Atomix fulfills their 500th order