Order Fulfillment Warehouse Setup: What You Should Know
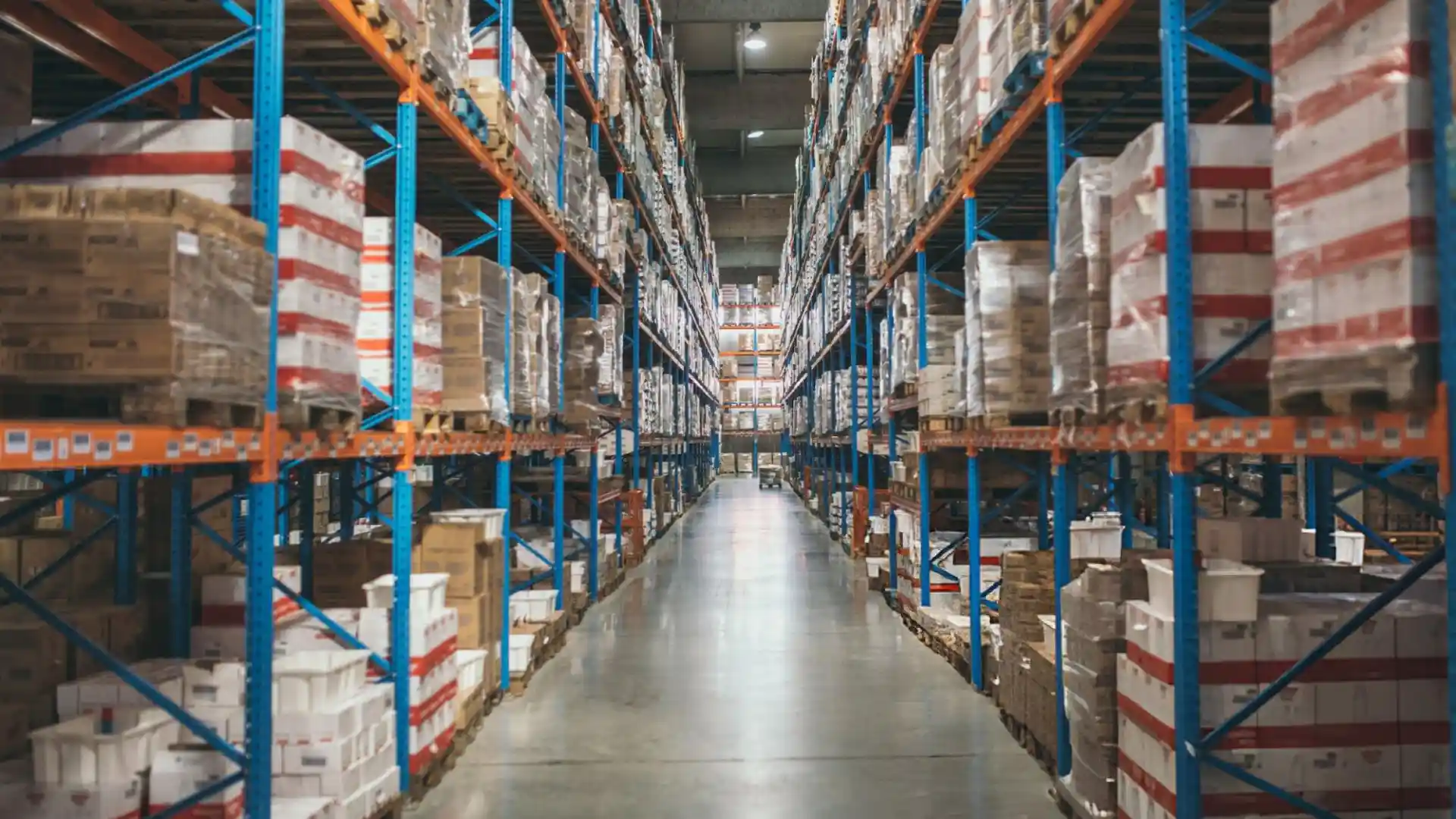
Establishing a well-structured order fulfillment warehouse is a core requirement for any ecommerce brand looking to scale operations, reduce errors, and improve delivery speeds. From layout planning and inventory management to software integration and third-party logistics (3PL) partnerships, each element contributes to the effectiveness of your overall fulfillment strategy.
This guide covers what brand decision-makers need to know when setting up an order fulfillment warehouse. Whether your business is preparing for its first physical warehouse or transitioning to a more advanced 3PL fulfillment model, this resource provides a step-by-step approach to building a warehouse system that supports ecommerce shipping efficiency, high order accuracy, and long-term growth.
Atomix Logistics is a trusted fulfillment partner that helps ecommerce brands establish seamless and scalable fulfillment processes. Through our full-service approach, we simplify everything from warehouse setup and order fulfillment software integration to inventory management and shipping logistics.
Why Warehouse Setup Matters for Order Fulfillment
A warehouse is not just a storage space. It is a core operational hub that controls how quickly, accurately, and cost-effectively a brand can deliver on customer expectations.
Here is what a well-planned warehouse setup directly affects:
- Picking and packing speed
- The layout and organization of inventory impact how quickly warehouse staff can locate and prepare items for shipment.
- Inventory accuracy
- Clear storage zones, smart inventory management systems, and barcode tracking reduce stockouts, shrinkage, and fulfillment errors.
- Fulfillment cost-efficiency
- Optimized workflows reduce labor hours and shipping mistakes, keeping overhead low and profit margins intact.
Understanding the Stages of Warehouse Setup
When setting up a warehouse for an ecommerce brand, the process typically breaks down into three stages:
1. Pre-Setup Planning
This is the stage where ecommerce decision-makers assess needs, define fulfillment goals, and align operational plans.
Key factors to evaluate:
- Order volume
- Daily order volume affects warehouse size, number of staff, and order fulfillment workflows.
- SKU complexity
- Brands with hundreds or thousands of SKUs require more sophisticated inventory zoning and tracking.
- Growth projections
- Planning for future demand ensures your warehouse layout and technology choices will scale with your business.
Atomix Logistics works closely with ecommerce brands during this phase, offering consultation and operational planning to map out space, technology, and shipping needs.
2. Physical Setup of Warehouse Infrastructure
This stage covers the physical components and logistics of creating a functional fulfillment environment.
Core components:
- Racking and shelving systems
- Choose between selective racking, pallet flow systems, or shelving depending on product size and velocity.
- Packing stations
- Designated areas for packing reduce time spent switching between tasks.
- Receiving and staging zones
- Dedicated zones for inbound inventory improve accuracy and prevent misplacement.
- Clear signage and labeling
- Visual cues help staff identify zones quickly, minimizing errors during picking.
- Warehouse safety compliance
- Follow OSHA and local regulations for safe storage, pathways, and equipment usage.
Atomix Logistics helps brands implement space-efficient infrastructure that reduces labor time and increases throughput.
3. Technology and Fulfillment System Integration
Manual tracking no longer supports ecommerce shipping demands. Fulfillment services require advanced software systems that enable real-time visibility and automation.
Systems to integrate:
- Order fulfillment software
- Connects ecommerce platforms with warehouse operations for seamless order processing.
- Warehouse Management System (WMS)
- Provides detailed tracking of inventory locations, movement history, and picking instructions.
- Shipping carriers and rate comparison tools
- Automates label printing and chooses the best carrier based on speed and cost.
- 3PL fulfillment tracking
- If working with a third-party logistics provider, ensure systems sync so inventory and orders update in real-time.
Atomix Logistics offers a fully integrated tech stack, including best-in-class WMS and multi-channel ecommerce fulfillment tools that eliminate delays and errors.
Order Fulfillment Strategies for Warehouse Efficiency
An optimized warehouse must support fast, accurate fulfillment while remaining adaptable to seasonal shifts and growth.
Zoning and Inventory Mapping
Grouping inventory based on picking patterns improves efficiency.
Common zoning strategies:
- ABC classification
- 'A' items are high-volume and should be closest to packing stations. 'C' items are slow-moving and can be stored in less accessible areas.
- Product type zones
- Group similar-sized or packaged items together to speed up pick times.
- Storage type zones
- Segregate pallets, cartons, and bin shelving areas for different SKUs.
Atomix Logistics customizes inventory zoning based on real order history and demand forecasting.
Batch and Wave Picking
These picking strategies reduce footsteps and manual errors.
- Batch picking
- Collects items for multiple orders in one run, then separates them during packing.
- Wave picking
- Groups orders by similar attributes like carrier or region to streamline sorting and shipping.
Cross-docking and Kitting
- Cross-docking reduces storage needs by moving inbound goods directly to outbound shipping.
- Kitting bundles multiple SKUs into one unit to simplify recurring orders.
These techniques work best with real-time order fulfillment software and coordinated inbound logistics.
Fulfillment Services vs. In-House: When to Use a 3PL
Running your own warehouse comes with full control but also greater risk and overhead. Partnering with a third-party logistics provider gives ecommerce brands access to fulfillment services without the capital expense of building internal systems.
Advantages of 3PL Fulfillment
- Scalability
- 3PL shipping networks grow with your business without requiring more space or staff.
- Speed to market
- Distributed fulfillment centers can reduce delivery zones and reach customers faster.
- Advanced systems
- Atomix Logistics uses industry-grade WMS and analytics tools that many brands cannot afford to build in-house.
- Cost savings
- Share costs of space, labor, and tech infrastructure across multiple brands.
Atomix Logistics specializes in ecommerce fulfillment and supports everything from DTC brand startups to enterprise-level clients seeking advanced 3PL shipping capabilities.
Choosing the Right Warehouse Setup Partner
Selecting a warehouse partner is a strategic decision. Whether building in-house operations or partnering with a 3PL fulfillment provider, the right support can impact long-term operational success.
Evaluation Checklist
- Track record with ecommerce brands
- Look for experience with businesses that match your size and order volume.
- Tech stack compatibility
- Ensure order fulfillment software, WMS, and ecommerce platform integrations work smoothly.
- Geographic coverage
- Proximity to customers can reduce shipping costs and transit times.
- Customer support
- Reliable communication and on-demand reporting tools help brands stay in control.
- Custom workflows
- Brands with specific packaging, kitting, or regulatory needs require a flexible warehouse for ecommerce brand fulfillment.
Atomix Logistics meets these criteria and provides tailored solutions that match your operational and strategic goals.
Tools That Power Smart Warehouse Fulfillment
The right software and tools reduce errors, improve visibility, and support scaling.
Must-Have Tools
- Real-time order tracking
- Connect your ecommerce platforms and provide customers with shipment updates instantly.
- Inventory management systems
- Monitor stock levels, restock alerts, and cycle counting to avoid overselling.
- Warehouse management system (WMS)
- Automates picking, packing, and shipping workflows for faster processing and lower error rates.
- Carrier integrations
- Access real-time shipping rates and generate labels with ease.
Atomix Logistics combines all these tools within a unified platform, giving brands full transparency and control across multiple sales channels.
Final Thoughts for Brands
A high-performing warehouse setup is not just about stacking shelves. It is about designing a system that supports the pace, precision, and performance expected by today’s ecommerce customers.
Whether planning an internal operation or partnering with a 3PL, success depends on:
- Strategic layout and zoning
- Integrated fulfillment technology
- Scalable processes and workflows
- Data visibility and control
Atomix Logistics stands out as a fulfillment services provider built for modern ecommerce. Our warehouse for ecommerce brand clients is optimized for speed, accuracy, and transparency, supporting growth at every stage.
Let Atomix Logistics be your fulfillment partner and take the guesswork out of warehouse setup.
Frequently Asked Questions About Order Fulfillment Warehouse Setup
What is involved in setting up an order fulfillment warehouse?
Setting up an order fulfillment warehouse involves choosing the right space, designing an efficient layout, implementing inventory management systems, and integrating order fulfillment software. Key steps include organizing racking and storage zones, installing packing stations, and establishing workflows that support fast and accurate ecommerce shipping.
How does a 3PL fulfillment provider improve warehouse operations?
A 3PL fulfillment provider like Atomix Logistics improves warehouse operations by offering scalable infrastructure, advanced order fulfillment software, real-time inventory tracking, and distributed shipping networks. Brands benefit from faster delivery times, reduced overhead, and access to professional logistics expertise without the cost of building internal systems.
What kind of technology is used in a fulfillment warehouse?
Modern fulfillment warehouses use a combination of order fulfillment software, warehouse management systems (WMS), barcode scanners, real-time inventory management tools, and carrier integration platforms. These technologies streamline picking, packing, shipping, and returns, helping ecommerce brands maintain high order accuracy and customer satisfaction.
Why is warehouse layout important for order fulfillment efficiency?
Warehouse layout directly affects how quickly and accurately orders are fulfilled. A strategic layout minimizes walking time, groups high-volume SKUs in accessible areas, and ensures clear zones for receiving, picking, and packing. Optimizing the layout supports faster ecommerce shipping and lower labor costs.
When should an ecommerce brand consider using a warehouse for fulfillment?
An ecommerce brand should consider using a warehouse for fulfillment when order volumes outgrow home-based or manual systems, when accuracy issues increase, or when scaling demands faster shipping and professional inventory control. Partnering with a 3PL like Atomix Logistics provides immediate access to warehouse space, fulfillment services, and expert support.
Talk with a team member and get $1,000 of order fulfillment credit*
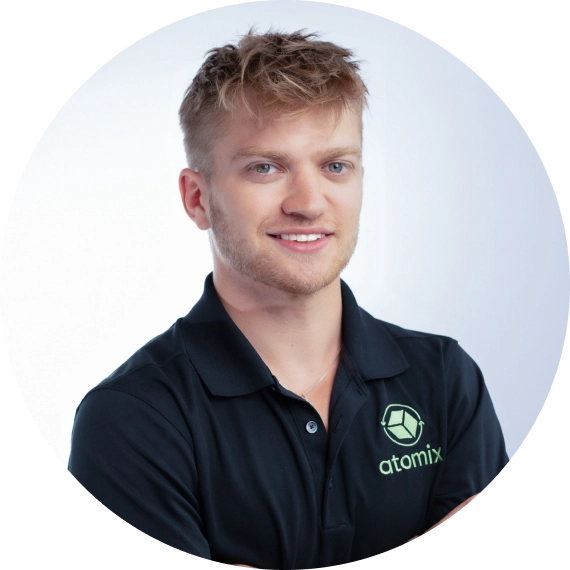
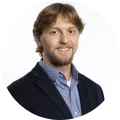
*$1,000 of credit is applied to customers account after Atomix fulfills their 500th order